The Opportunity
For years, drywall placement has relied on manual 2D planning, where standard board sizes are used without fully considering material optimization. While this approach is familiar, it often results in excessive offcuts, unnecessary material waste, and increased costs. On large-scale projects, the impact of these inefficiencies is significant. The question is: how do we ensure minimal waste while maintaining installation efficiency? Traditional methods rely on intuition, but without a data-driven approach, designers often miss the true optimal solution.
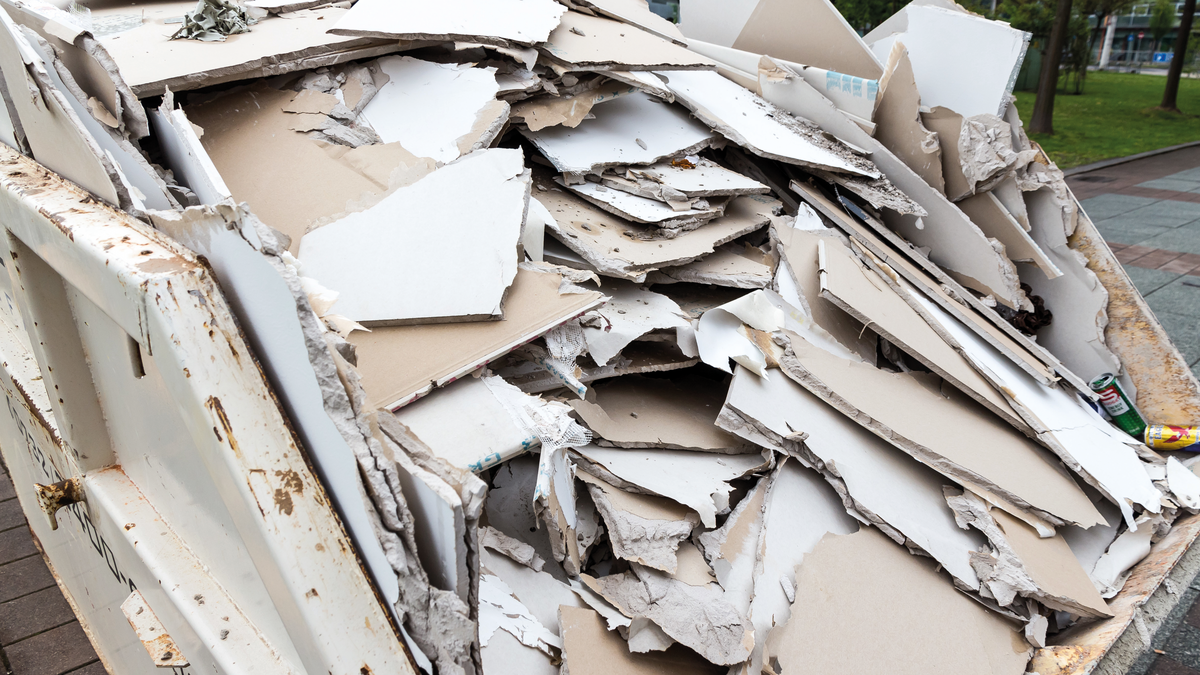
The KOPE Approach
On a recent project with British Gypsum (BG), KOPE demonstrated its powerful optimization capabilities by analyzing three drywall boarding scenarios:
1. Using a single standard board throughout
2. Using a bespoke board to match wall height
3. Running KOPE’s optimization engine to find the most efficient board size
Rather than relying on assumptions, KOPE ran thousands of possible layout scenarios in seconds to determine the board configuration that would minimize waste while keeping installation efficient. The result? A bespoke 2060mm board reduced waste by 55% compared to a standard board, with only six additional pieces required per floor.
.png)
The Impact
The optimized 2060mm board was a solution that would never have been suggested manually. Not only did it significantly cut waste, but it also balanced efficiency and practicality.
To put this into perspective:
• The waste saving per floor was 220m², equivalent to 77 full drywall boards (nearly two pallets’ worth).
• Over 18 floors, that translates to 29 pallets of drywall saved from landfill—equivalent to nearly two full articulated lorries of material .
In carbon terms that’s roughly equivalent to:
• Approximately 180 tree seedlings grown for 10 years, as each tree can sequester about 60 pounds (27 kg) of CO₂ annually.
• Driving a typical passenger vehicle for about 27,000 miles (43,500 km), assuming an average emission of 404 grams of CO₂ per mile
By leveraging KOPE’s AI-driven optimization, this project achieved significant waste reduction and lower material costs, alongside a streamlined installation process. Traditionally, projects relying on standard methods would involve simply delivering pallets of drywall, leading to substantial on-site cutting and waste after a typical take-off in tools like Bluebeam or OST. While some waste-conscious companies might consider drawing detailed drywall layouts in 2D CAD to optimize material use, the time investment required makes this approach impractical for most. KOPE offers a solution, providing waste optimization and material efficiency without the prohibitive manual effort previously necessary.
Conclusion
This case study highlights the power of KOPE’s optimization technology in automating material efficiency, therefore eliminating guesswork, reducing environmental impact, and cutting project costs. By running thousands of layout variations in seconds, KOPE enables teams to make data-driven decisions at scale. With industry leaders like British Gypsum adopting KOPE, the future of construction is no longer about intuition — it’s about precision, optimization, and automation.
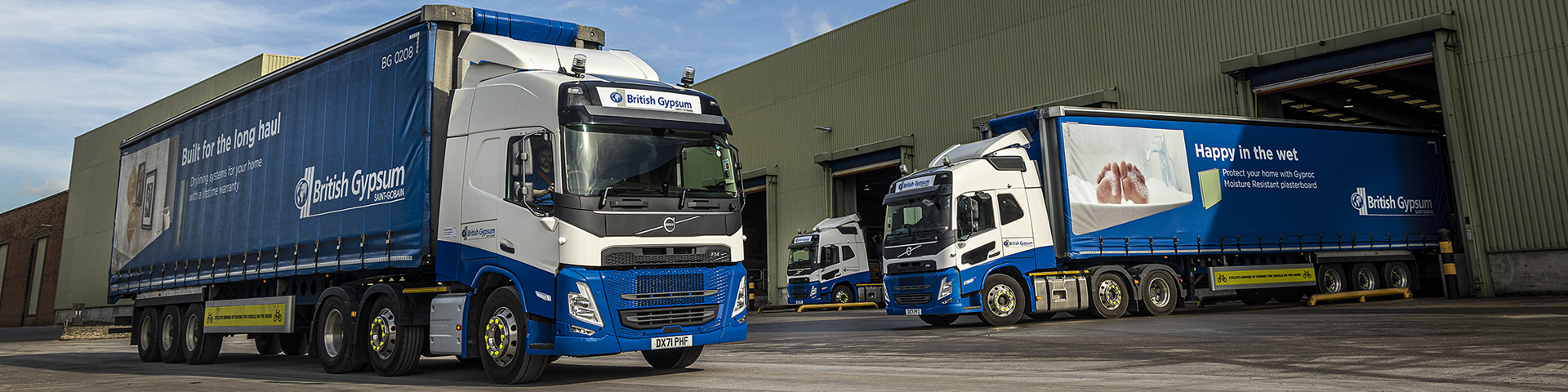
For context, here are some equivalent waste weights for 29 pallets of drywall :
14,500 kg (~14.5 metric tonnes) of drywall waste saved =
🏢 5.8 fully grown African elephants (~2.5 tonnes each)
🚍 One full-size London double-decker bus (~14.5 tonnes)
✈️ A small private jet (e.g., Cessna Citation M2, ~14 tonnes)
🥔 290 sacks of potatoes (50 kg per sack)
🚗 9 mid-sized cars (~1.6 tonnes each, e.g., Volkswagen Golf)
🏋️ 1,450 Olympic barbells (10 kg each)
🎄 725 Christmas trees (~20 kg per tree)
🧱 Over 11,000 standard clay bricks (~1.3 kg each)
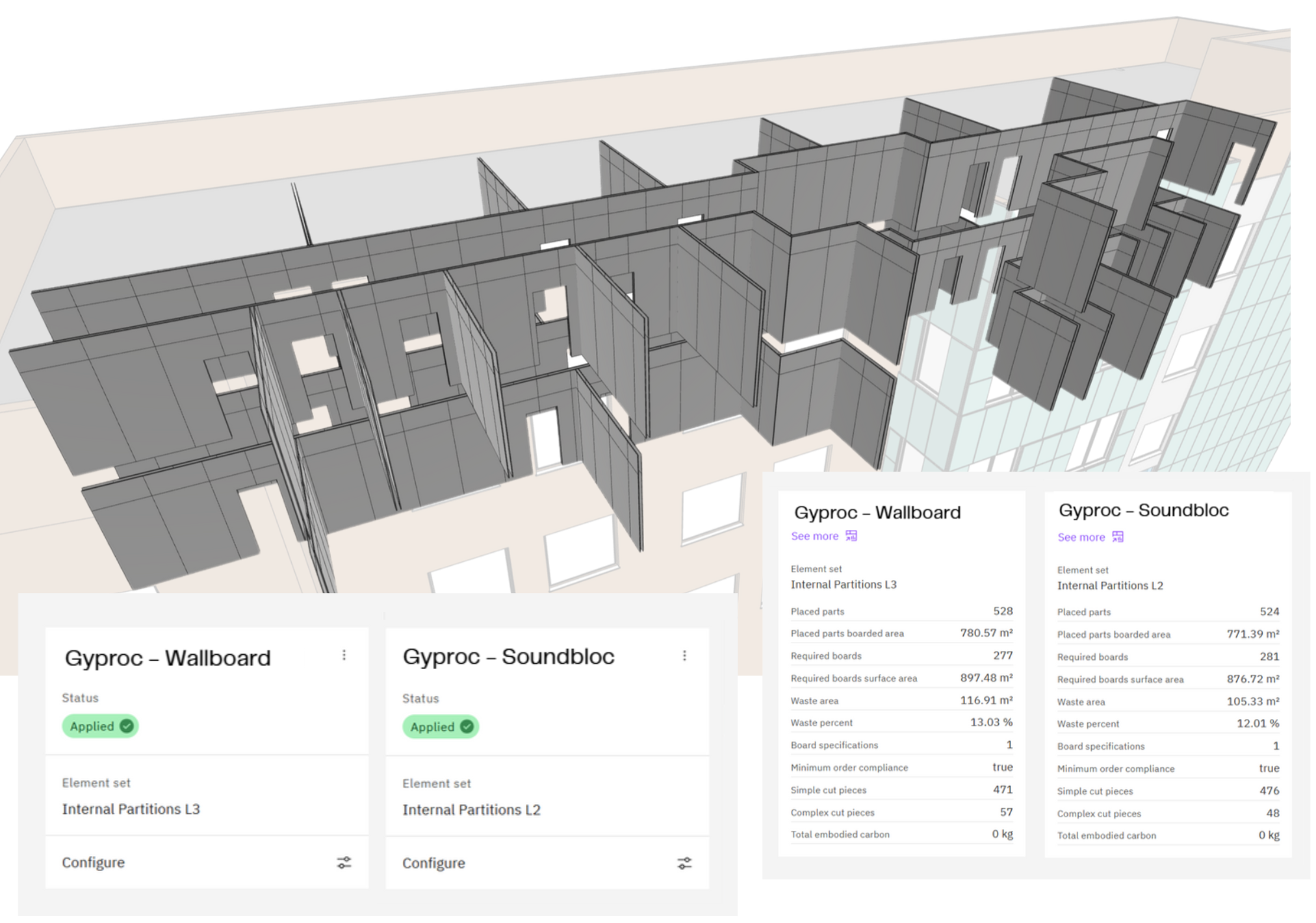
This puts into perspective just how much material KOPE’s optimization can prevent from going to landfill—helping both the environment and the bottom line.