Intro
KOPE enables Addazu to deploy rapid design cycles and generate instant 3D models using their kit of parts. This enhances their clients' understanding of how this sophisticated prefabricated kit of parts can improve their project by decreasing development costs and increasing the developers' profit margins.
Outcome: A 100x reduction in time required to configure architectural designs using the Addazu proprietary prefab building system. Resulting in an estimated $350,000 in design related OPEX cost savings per year for Addazu
The opportunity
Addazu's modular wall panel system offers adaptable, reconfigurable components that ensure rapid on-site assembly, minimal site disruption, and reduced insurance costs. The Addazu steel-framed panels arrive flat-packed as integrated cassettes with structural framing and exterior sheathing to provide consistent quality, durability, energy-efficient building envelopes, and versatile design possibilities. They significantly outperform traditional construction methods in speed, affordability, and sustainability
While Addazu’s system solves many problems for teams once on site, they were faced with the challenge of configuring their panels on new project designs. For a single-family house project, Addazu was spending upwards of 40 hours per project placing panels and adjusting window and door opening sizes to fit their system, to minimise the need for costly bespoke panels. While Addazu's system solves many problems for teams once the panels arrive on-site, Addazu was challenged by increased design costs to configure their panels for new projects, which were eventually passed on to the client.
Continued adjustments, adaptations, and versioning presented various issues, from scheduling multiple design reviews, increased communication with clients and Architectural teams, and version control. Addazu approached KOPE to significantly improve this process and support their efforts in estimating projects faster and targeting more significant building types without dramatically increasing time and labor costs.
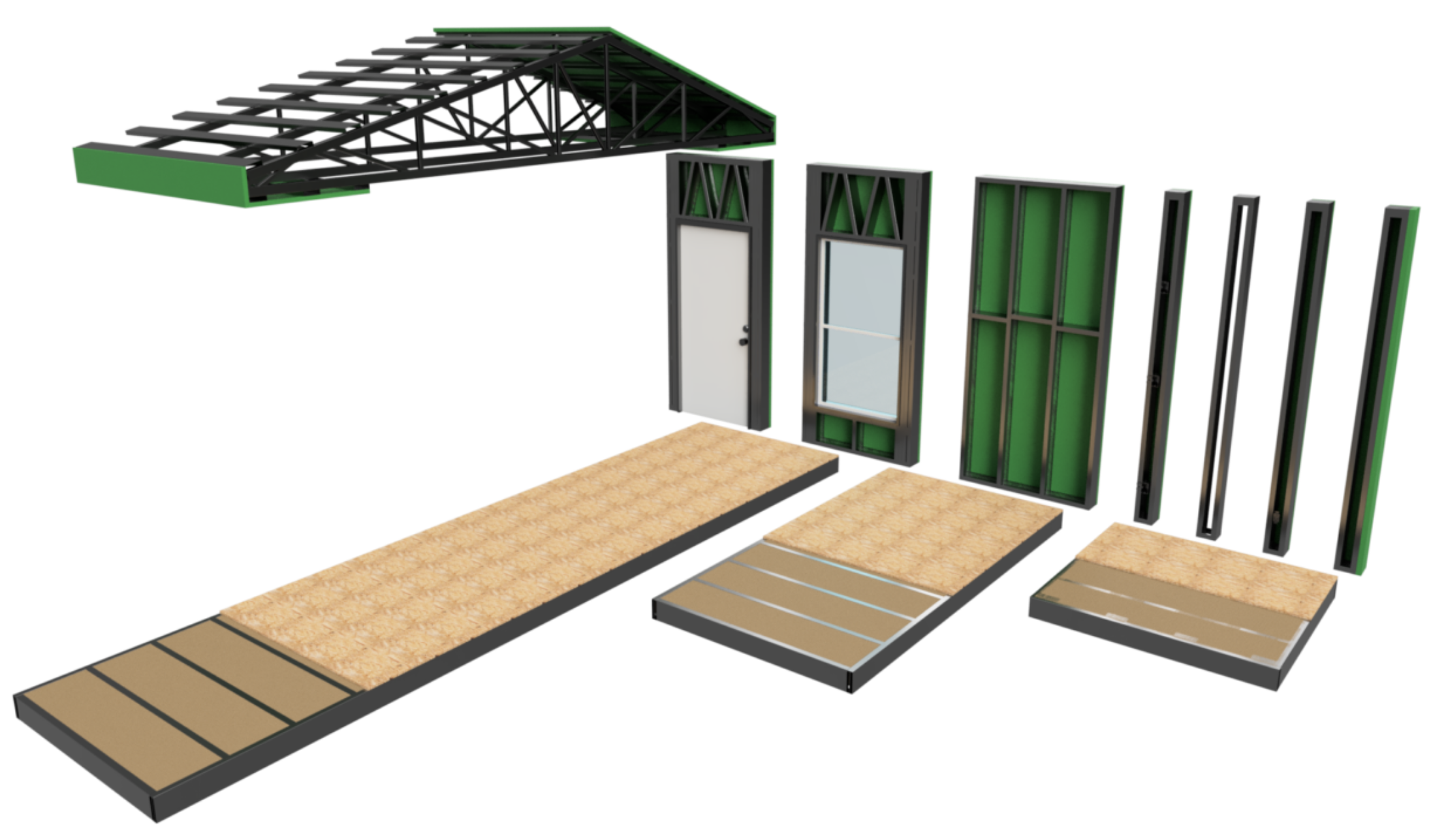
The system
Addazu's modular wall system is made from a catalogue of standard-sized and bespoke panels. A project benefits significantly when more standard panels are used and the need for bespoke panels is designed out of the project.
Once Addazu’s design team receive a project, they iterate through the design making small adjustments to window and door opening positions, to increase the number of standard panels being used. These adjustments are shared with the project design and ownership teams, and are either accepted in full, partially or not at all to better predict their manufacturing pipeline.
For a 1,000 to 1,500 sq. ft single-family home, this process can take 40+ hours and required a skilled user with expert understanding of the system. The 100s of possible placement scenarios possible can be overwhelming, and an opportunity to optimize could be missed.

The KOPE solution
Working with our technical specialist team, KOPE codified the design, adjustment and placement logic of the Addazu system. Enabling panels to be placed automatically using KOPE’s Configuration engine is a huge time saving over manual placement of panels into a design file.
KOPE places panels to Addazu’s optimal grid spacing, identifying where window and door openings land in relation to this grid, and immediately identifying when standard and bespoke panels are needed. With this, Addazu have an “As-Designed” solution, but often with many bespoke panels as a result. KOPE allows for refinement by offering two strategies to improve the standardisation.
1. Adjust the opening sizes to the nearest standard grid position – By increasing or decreasing the opening to it’s closest grid line, Addazu can remove the largest number of bespoke door and wall panels from the design.
2. Maintain the opening size but relocating to the closest standard grid position – Maintaining the bespoke opening sizes often requires a bespoke panel, but by adjusting it’s position to a grid location, the infill panels can benefit from a standard panel.
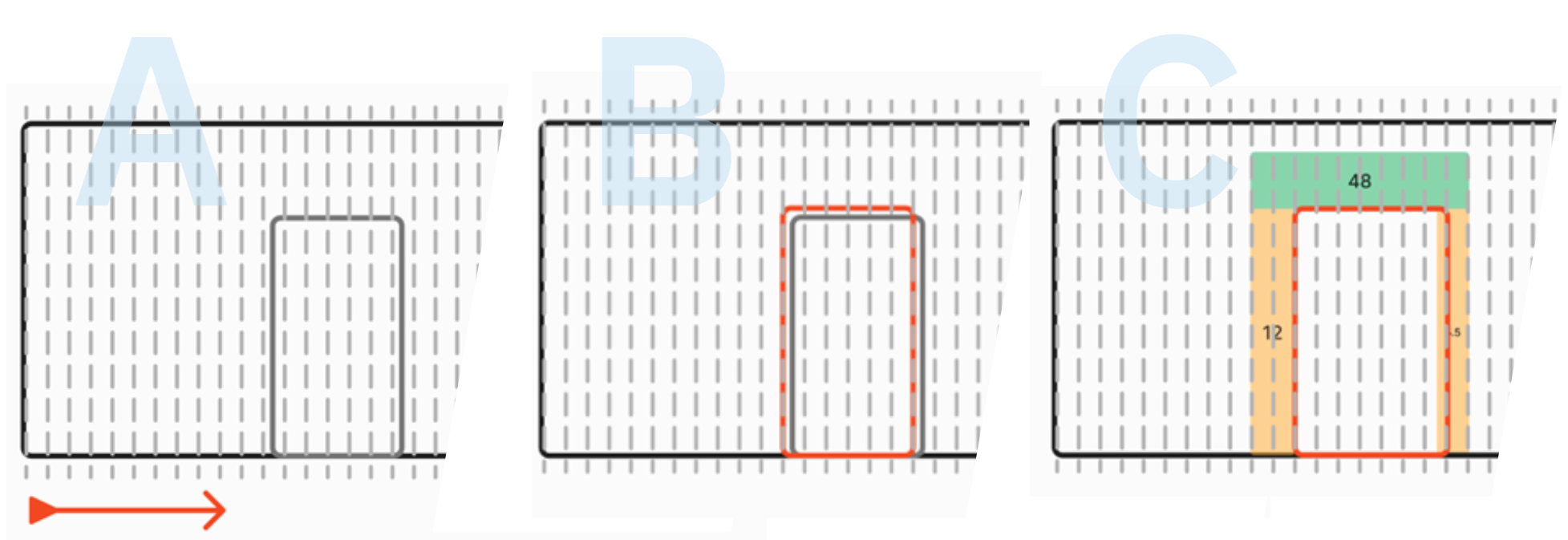
Within 15 minutes, Addazu have generated three district solutions with the panels that can be coordinated with the project team to identify the best approach going forward.
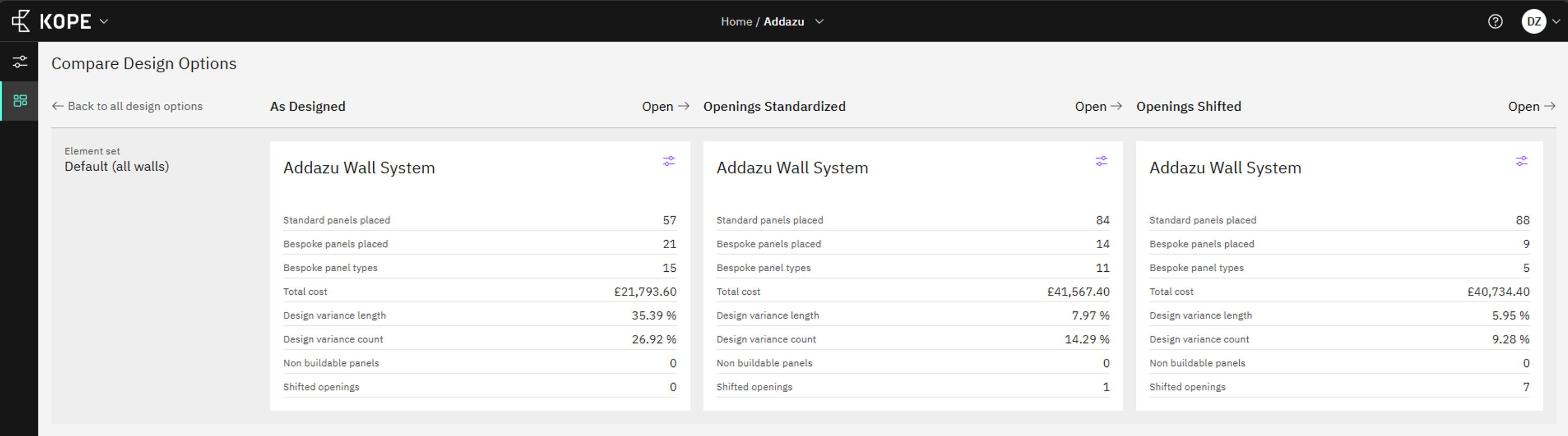
Addazu on KOPE
By using KOPE, Addazu greatly improves the speed and accuracy of their panel configuration process and can now return multiple solutions to their customers in record time. With the design time minimized, Addazu can quote more projects, bid on larger projects and more easily communicate the value of their sophisticated standardization method.
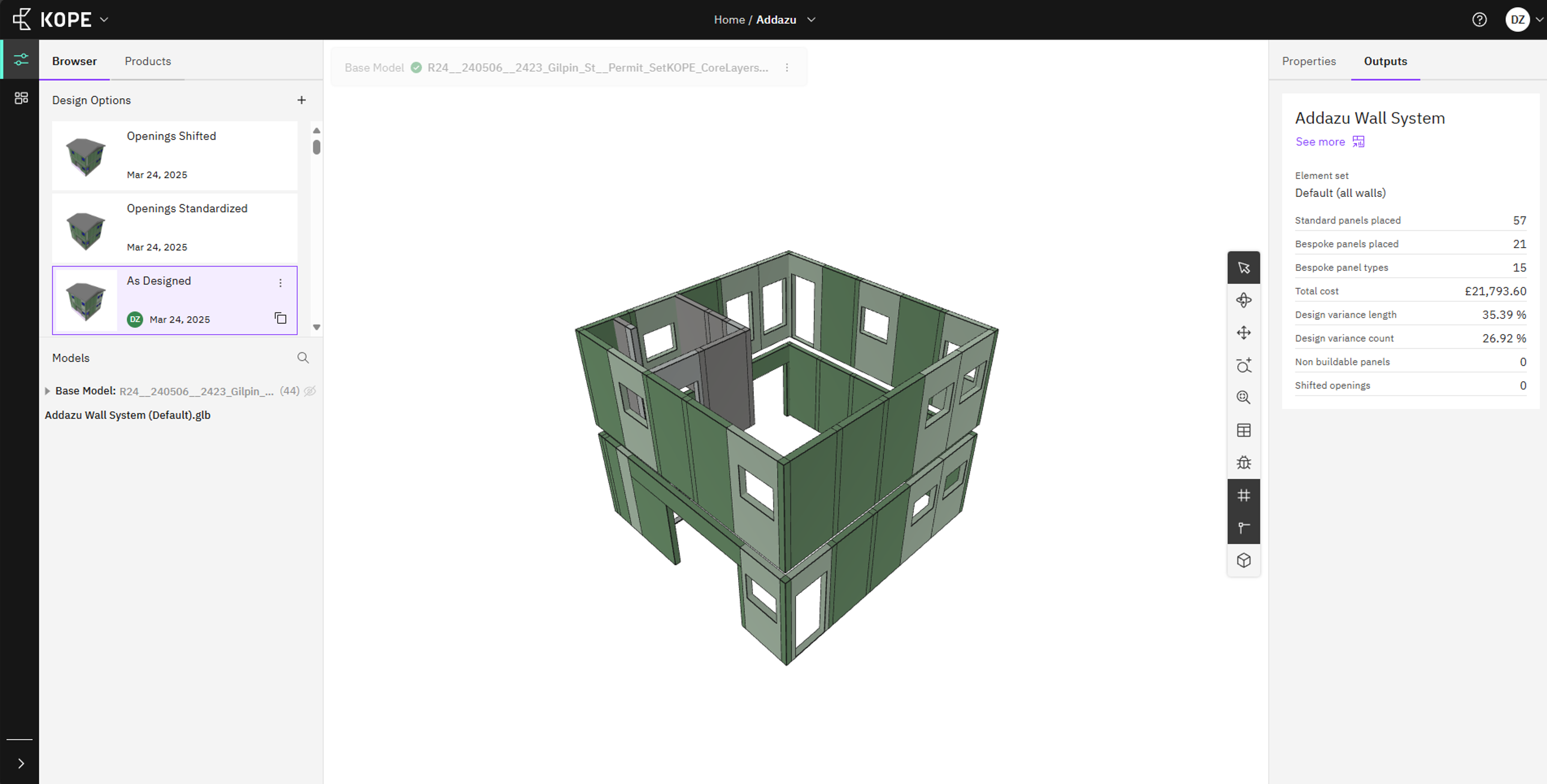
"KOPE has allowed our team to be nimble, proactive, and agile in responding to our customers' needs. By implementing the KOPE software, Addazu can conduct real-time design iteration meetings, produce detailed estimates in minutes, and reduce our design-related OPEX expenses by over 75%." - Kelly Pickering, Founder.
KOPE is the only purpose built solution for Kit of Part manufacturers like Addazu. By understanding their design systems, manufacturing limitations, and project objectives, KOPE is fundamentally changing how kits of parts are integrated into construction projects.